The Right Chemistry
Nickel-zinc batteries promise to fill the performance gap of lead-acid and lithium-ion batteries. Craig Wilkins, president and CEO of Battery Grade Materials, explains how.
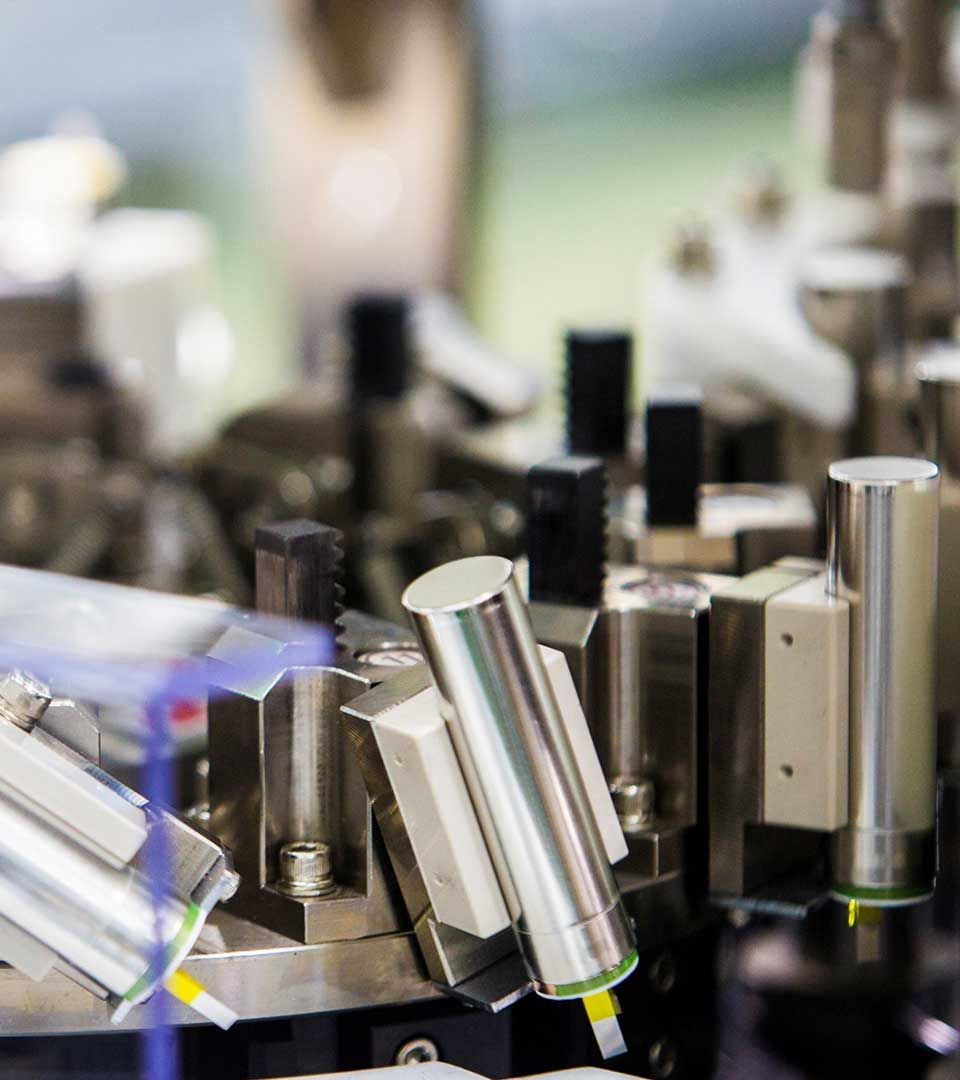
The energy storage sector has always relied on lead-acid and lithium-ion batteries but evolving technology has exposed gaps in the performance of these batteries over the past few years. Lead-acid batteries have been known to fall short on capacity, power, and life as more consumers seek longer run times in smaller packages. Lithium-ion packs on the other hand, have proved to be costly requiring nothing lower than $200/kwh, mostly stemming from the advanced operations needed to make these batteries. Moreover, fires due to lithium-ion batteries have raised questions on their safety too.
A new alternative
With the total market for batteries in the energy storage sector expected to reach 2.5TWh by 2030, there is room for more players and chemistries to fill the gap left by the two most used battery chemistries today, giving rise to unique chemistries like nickel-zinc.
Craig Wilkins, president and CEO of Battery Grade Materials, a company that produces nickel-zinc batteries makes the case for these batteries. “Zinc batteries are the best story around energy storage and sustainability,” he says, adding that zinc is one of those unique materials where the benefits outweigh the challenges.
Speaking at the International Zinc Association’s Zinc Conference in Scottsdale, Arizona in March, Wilkins noted some of these benefits. “Zinc is a low-cost resource, is globally abundant, has high density, which is perfect for battery performance grades, is safe and most importantly easily and cost-effectively recyclable through low energy processes.
It is these benefits that led AeSir Technologies, where Wilkins is also the CFO, carve out Battery Grade Materials (BG Materials) to develop nickel-zinc battery technology that uses recycled materials. The realization came when “we were about to announce our first gigafactory in the United States and faced the challenge of procuring raw materials at the levels we were going to need to supply the factory’s production,” says Wilkins.
He adds that nickel metal hydride, which forms the base chemistry of these batteries was never at the commercial scale that AeSir intended to be, which resulted in a very few suppliers. “BG was really spun out with the vision of supporting AeSir and its licensee partners with the raw materials needed to construct nickel zinc batteries.”
BG is also developing new technologies and processes to make the recycling of zinc and nickel for their batteries a low-carbon one. “We want to make our product sustainable and that not only includes buying raw material that comes from sustainable mining, but also staying away from high heat smelting processes that consume a lot of energy,” Wilkins explains. “We have taken a new approach in metallurgical processes to reduce that carbon footprint because our end-customers, who consist of data centres and telecom companies demand it.”
Competing chemistries
Still, lithium-ion and lead-acid batteries are formidable competitors. The former’s demand is not only growing in the end-consumer segment but also for electric vehicles (EVs). Wilkins concedes that these chemistries have been wildly successful and remain the most used battery packs for the energy storage sector too. “However, we believe there’s no one perfect battery for every application, especially with technology evolving at such a fast pace,” he notes.
Giving the example of automobiles and cell phones, he says that if one wants the power to go from 0-60 in 3.2 seconds, lithium is the right battery, if you want to build a cell phone, then powerful lithium is a great technology. But because it is commercially viable and technologically advanced, companies have tried to put it everywhere—even in applications where other chemistries are more viable.
“There’s no one perfect battery for every application,” Wilkins opines. “While lithium might be great for many applications, companies forget that like other metals it is a finite resource. As the market demand grows there will be a scarcity of reserves. That is where we want to be a better purveyor of resource allocation for certain battery technologies that fit in one spot and not the other.”
This is where, he feels nickel-zinc batteries could be the disruptor. “We have lead-acid batteries on one end of the batteries spectrum and lithium-ion on the other. Nickel-zinc fits right in the middle. It is a great industrial battery that does not create fire issues, has a lower cost of producing than the other two chemistries, and can carry twice the energy density and last twice as long,” Wilkins says.
Chemistry consumption of nickel-zinc batteries
*SEE TABLE BELOW
Accepting the alternative
However, the acceptance of nickel-zinc batteries has also come with its own set of challenges. “Everyone has known for a long time that nickel-zinc is a high-powered battery, but it had lifecycle issues because of the type of zinc anodes being used for the zinc chemistry,” Wilkins says. “No one dedicated efforts on fixing this flaw and AeSir was founded to find an answer to this issue.”
He adds that as a zinc-based batteries company, AeSir dedicated three years perfecting their zinc anode chemistries and once that was accomplished, they moved to nickel to make these batteries commercially viable.
Today, the company is tackling the challenge of unsustainable mining, which, according to Wilkins is the more pressing issue that can impact supply chains in the long term.
“The supply chain issues over the past two years really relate to the COVID-19 pandemic,” Wilkins observes. “At that time, for example, the supply time for LG Chem to ship batteries to data centres went from three months to nine months, but those lag times are reducing. Lead-acid batteries that were on a six-month backlog are now at two months. These issues were more related to labour than raw supply issues.”
However, with the number of battery gigafactories planned over the next two years, he explains, the amount of raw materials consumption coming out of the earth is certainly going to create supply chain issues. “Everyone right now is going to the easiest resource and that is chopping up the earth to get as much metal out of the ground for significant kickbacks. Eventually there will be a public outcry against these practices, which is why it is necessary to seek that balance now, rather than later,” Wilkins says.
Still, the need for batteries is set to grow exponentially over the next few years and the industry needs to be ready for it. “Our long term objective should be to seamlessly transition into the electron economy and to achieve great innovation in this space we must have a catalyst,” he says.
Wilkins views the energy storage space as that catalyst. “Energy storage is not only going to be here for a long time, but we will see exponential growth regardless of electric cars taking that 50pc of the automotive industry; there is just that much demand coming from other sectors.”
Recycling plays its part
Recycling will play an important role in the battery space regardless of the chemistry. Although, Wilkins hopes to see the carbon-footprint of high heat smelters that are currently used for lead recycling, reduce as more chemistries come into play.
He believes that moving forward recycling, or urban mining as many call it, is going to be the most critical area to extract metals and reprocess them to battery grade material. “I don’t want to just recycle material, but rather reprocess material that is battery grade, simply because as battery makers and recyclers we are required by end-consumers to ensure that material used in batteries will come back into the battery supply chain, rather than being used elsewhere.”
He concludes that if one can cost-effectively pull battery-grade material through a closed loop system, there will be enough to support the envisaged growth in this sector as recycling will help the matter circle back on itself.
Chemistry | Number of Batteries | Nickel-Zinc Chemistry | |
---|---|---|---|
Chemistry/Battery | 1 | 5.982 kg (Zinc-Oxide) | 4.695 kg (Nickel-Hydroxide) |
Chemistry per MWh | 500 | 2,991 kg (Zinc-Oxide) | 2,347 kg (Nickel-Hydroxide) |
Chemistry per GWh | 500,000 | 2,991,000 kg (Zinc-Oxide) | 2,347,000 kg (Nickel-Hydroxide) |
Metric Tons / TWh | 500,000,000 | 2,991,000 (Zinc-Oxide) | 2,347,000 (Nickel-Hydroxide) |
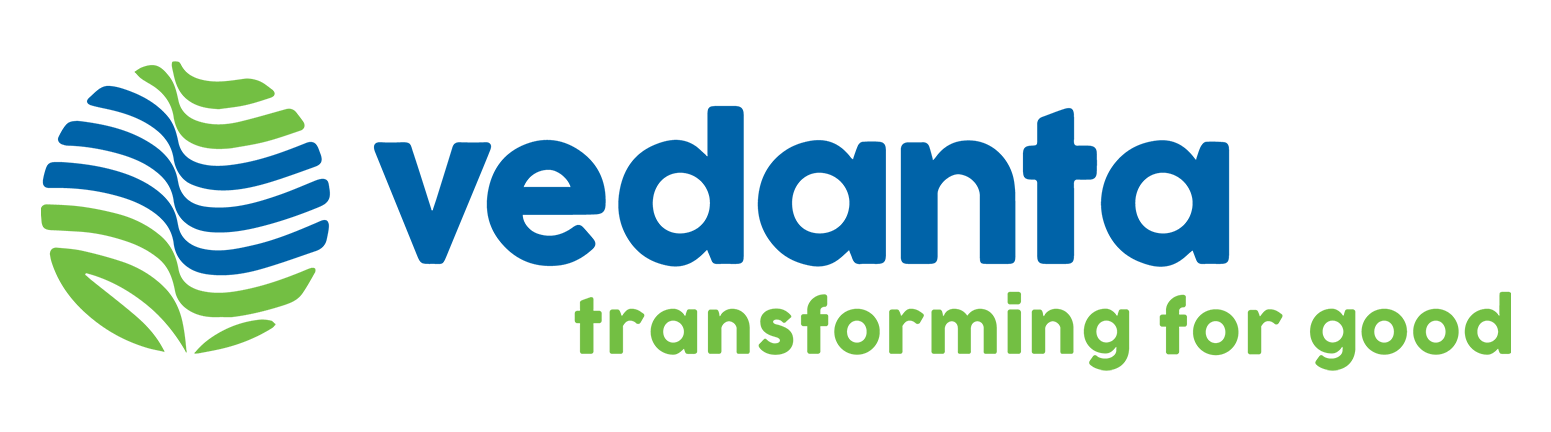
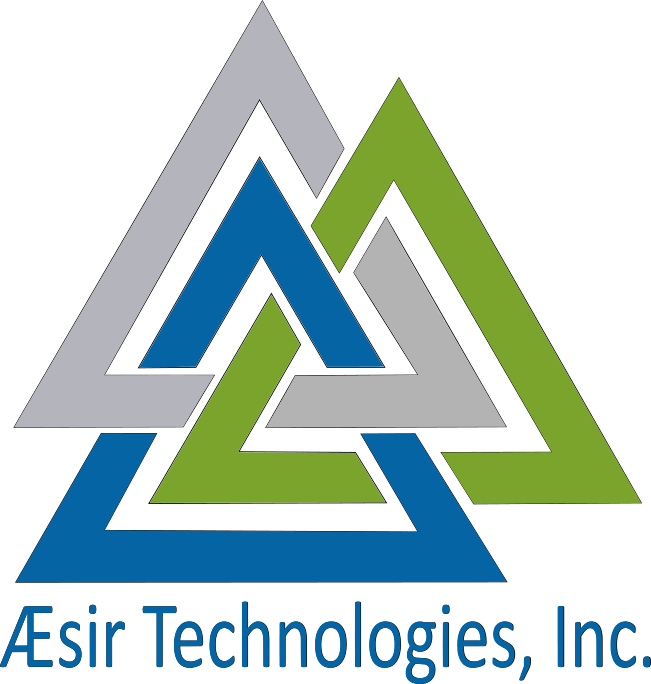